තාප හැකිලීමේ චිත්රපට ලේබල්විශේෂිත තීන්ත භාවිතයෙන් ප්ලාස්ටික් පටල හෝ නල මත මුද්රණය කර ඇති තුනී පටල ලේබල් වේ. ලේබල් කිරීමේ ක්රියාවලියේදී, රත් වූ විට (70 ℃ පමණ), හැකිලීමේ ලේබලය ඉක්මනින් කන්ටේනරයේ පිටත සමෝච්ඡය දිගේ හැකිලෙන අතර බහාලුම් මතුපිටට තදින් ඇලී සිටී. තාප හැකිලීමේ චිත්රපට ලේබලවල ප්රධාන වශයෙන් shrink sleeve ලේබල් සහ හැකිලීමේ ලේබල් ඇතුළත් වේ.

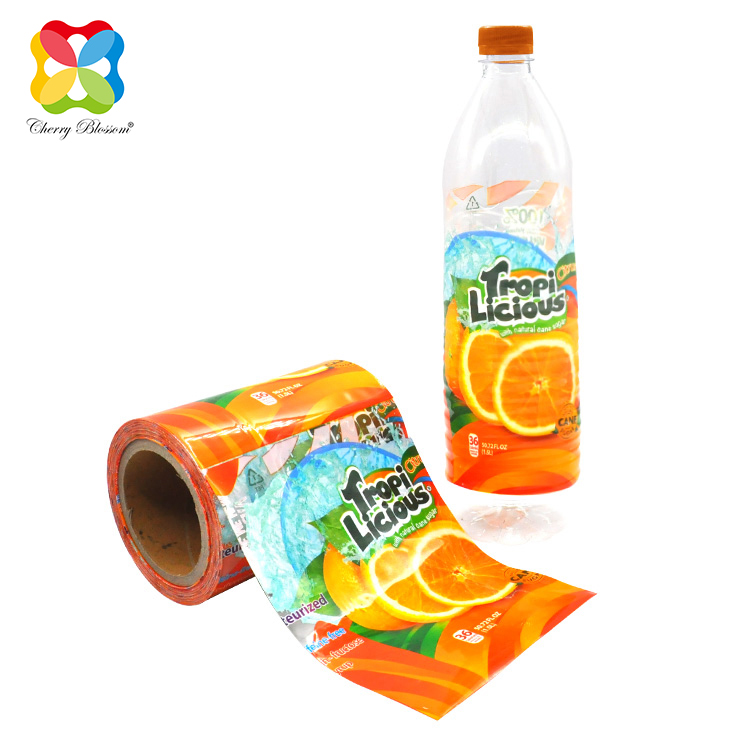
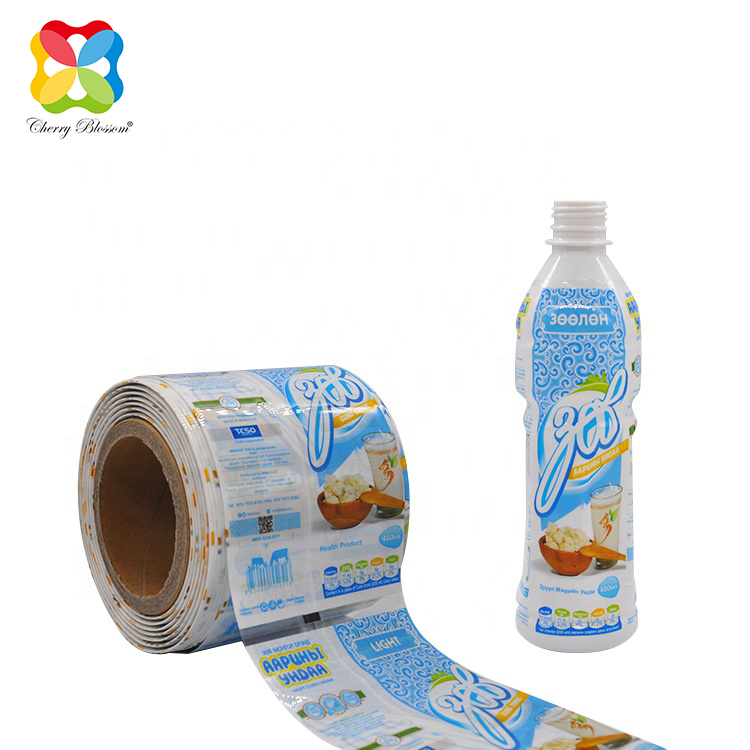
ක්රියාකාරී ලක්ෂණ
හැකිලීමේ අත් ලේබලය යනු තාප හැකිලීමේ පටලයකින් උපස්ථරය ලෙස සාදන ලද සිලින්ඩරාකාර ලේබලයකි, එය මුද්රණය කර පසුව සාදනු ලැබේ. එය පහසු භාවිතයේ ලක්ෂණයක් ඇති අතර විශේෂ හැඩැති බහාලුම් සඳහා අතිශයින්ම සුදුසුය. මුද්රිත ලේබලය කන්ටේනරය මත ආවරණය කිරීම සඳහා Shrink sleeve ලේබල් වලට සාමාන්යයෙන් විශේෂිත ලේබල් කිරීමේ උපකරණ අවශ්ය වේ. පළමුව, ලේබල් කිරීමේ උපාංගය මුද්රා තැබූ සිලින්ඩරාකාර අත් ලේබලය විවෘත කරයි, සමහර විට විදුම් අවශ්ය විය හැකිය; ඊළඟට, ලේබලය සුදුසු ප්රමාණවලට කපා කන්ටේනරය මත තබන්න; එවිට කන්ටේනරයේ මතුපිටට ලේබලය තදින් ඇමිණීම සඳහා තාප පිරියම් කිරීම සඳහා වාෂ්ප, අධෝරක්ත කිරණ හෝ උණුසුම් වායු නාලිකා භාවිතා කරන්න.
චිත්රපටයේ ඉහළ විනිවිදභාවය හේතුවෙන්, ලේබලය දීප්තිමත් සහ දීප්තිමත් වර්ණයක් ඇත. කෙසේ වෙතත්, භාවිතයේදී හැකිලීමේ අවශ්යතාවය හේතුවෙන්, විශේෂයෙන් තීරු කේත සලකුණු සහිත මුද්රණය කරන ලද නිෂ්පාදන සඳහා, රටා විකෘති කිරීමේ අඩුපාඩුවක් ඇත. දැඩි සැලසුම් සහ මුද්රණ තත්ත්ව පාලනය සිදු කළ යුතු අතර, එසේ නොමැති නම් රටාවේ විරූපණය තීරු කේතයේ ගුණාත්මක භාවය නුසුදුසු වීමට හේතු වේ. සම්ප්රදායික ලේබල් කිරීමේ උපකරණ භාවිතයෙන් හැකිලීමේ ලේබල් ලේබල් කළ හැකි අතර, ලේබල් කිරීමේ ක්රියාවලියේදී මැලියම් සහ ඉහළ උෂ්ණත්වයන් භාවිතා කිරීම අවශ්ය වේ. හැකිලීමේ ක්රියාවලියේදී, චිත්රපටයේ අතිච්ඡාදනය වන කොටස්වල ඇති මැලියම් මගින් ඇතිවන ආතතිය හේතුවෙන් උණුසුම් දියවන මැලියම් වඩාත් කැමති වේ.
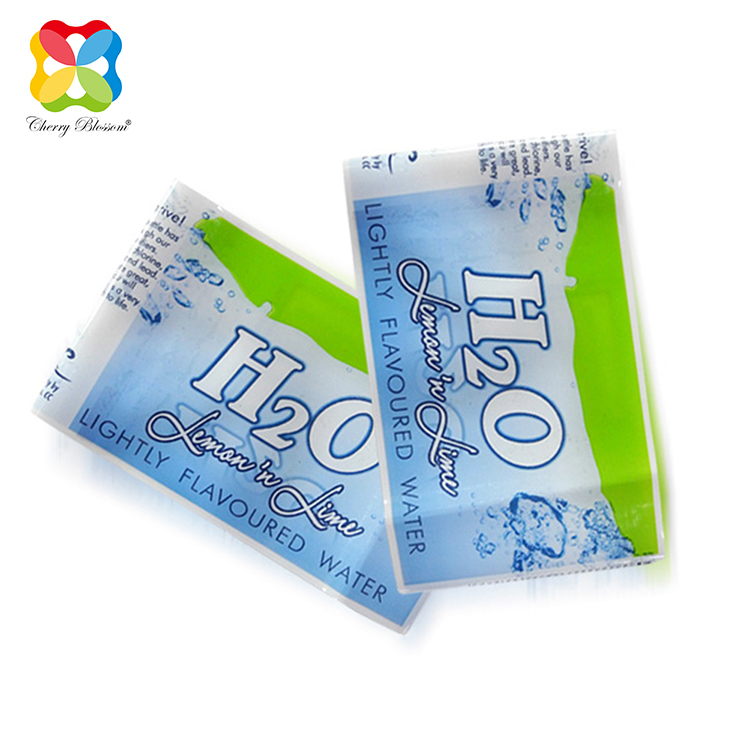
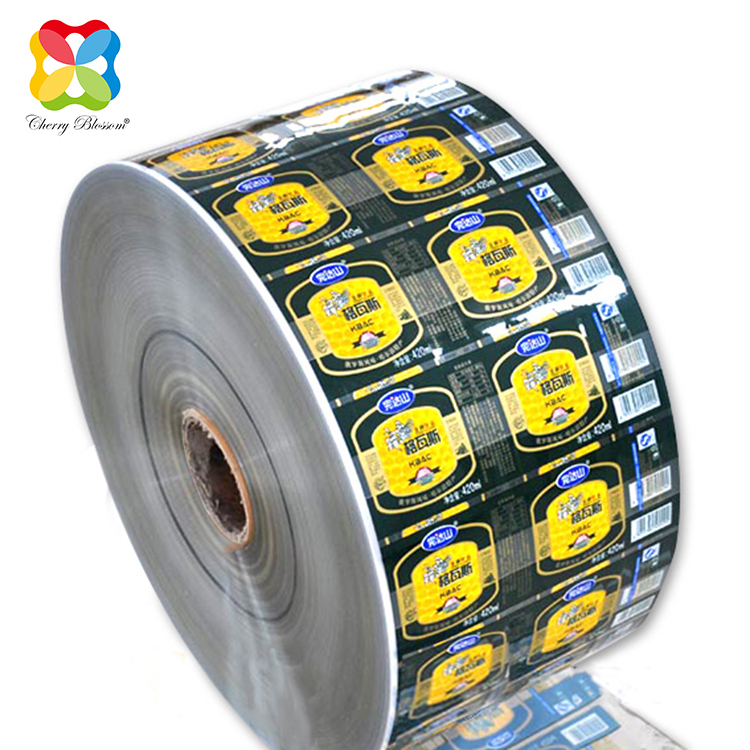
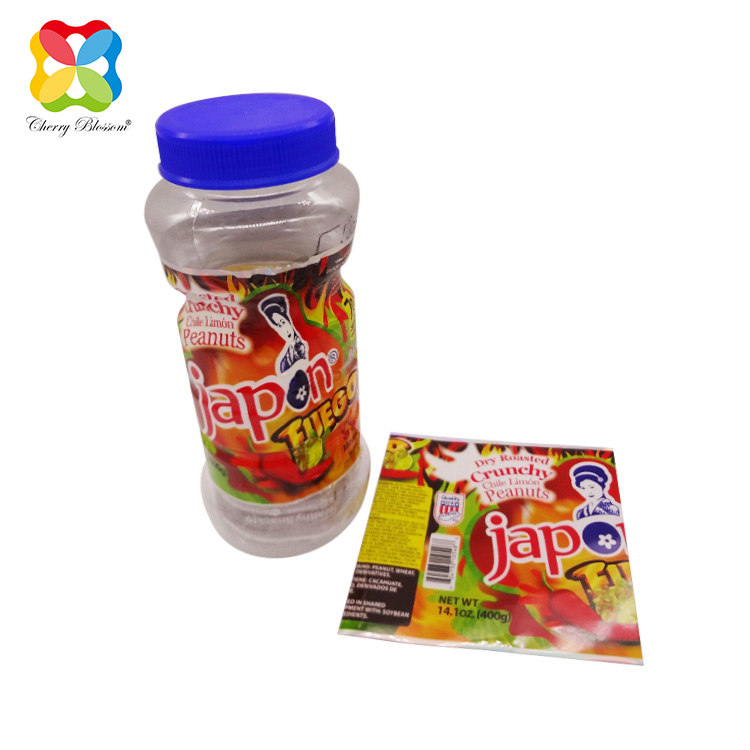
Prepress නිෂ්පාදනය
තාප හැකිලීමේ පටලය තාප ප්ලාස්ටික් පටලයක් වන අතර එය නිෂ්පාදනයේදී දිගු කිරීමෙන් දිශානතියට පත් වන අතර භාවිතයේදී හැකිලී යයි. එබැවින්, මුද්රණය සඳහා කුමන මුද්රණ ක්රමයක් භාවිතා කළත්, මතුපිට රටාව සැලසුම් කිරීමට පෙර, ද්රව්යයේ තිරස් සහ සිරස් හැකිලීමේ අනුපාත මෙන්ම හැකිලීමෙන් පසු අලංකාර ග්රැෆික්ස් සහ පෙළෙහි විවිධ දිශාවන්හි අවසර ලත් විරූපණ දෝෂ සලකා බැලිය යුතුය. කන්ටේනරය මත හැකිලී ඇති රටාව, පෙළ සහ තීරු කේතය නිවැරදිව ප්රතිසාධනය කිරීම සහතික කිරීම සඳහා.
රටාවේ දිශාව
තාපය හැකිලීමේ පටලය මුද්රණය කරන්නේ gravure printing හෝ flexographic මුද්රණය භාවිතයෙන් වුවද, එහි මුද්රණය ප්රධාන වශයෙන් අභ්යන්තර මුද්රණ ක්රමයේ සිදු වන අතර මුද්රණ තහඩුවේ රටාවට සාපේක්ෂව දිශාව ධනාත්මක විය යුතුය. වර්තමානයේ මතුපිට මුද්රණය සඳහා හැකිලෙන චිත්රපට ද තිබේ. මෙම අවස්ථාවේදී, මුද්රණ තහඩුව මත රටා දිශාව ආපසු හැරවිය යුතුය.
රටා වල ධුරාවලිය
flexographic මුද්රණයේ ඇති සීමාවන් හේතුවෙන්, flexographic මුද්රණය භාවිතයෙන් හැකිලීමේ චිත්රපටය මුද්රණය කරන්නේ නම්, රූපයේ මට්ටම ඉතා සියුම් නොවිය යුතු අතර, gravure මුද්රණය භාවිතා කිරීමේදී වඩාත් පොහොසත් මට්ටමේ රූපයක් අවශ්ය විය හැකිය.
මානයන් සැලසුම් කිරීම
මුද්රණය සඳහා භාවිතා කරන තාප හැකිලීමේ චිත්රපට ද්රව්යයේ තීර්යක් හැකිලීමේ අනුපාතය 50% සිට 52% දක්වා සහ 60% සිට 62% දක්වා වන අතර විශේෂ තත්වයන් යටතේ 90% දක්වා ළඟා විය හැකිය. කල්පවත්නා හැකිලීමේ අනුපාතය 6% සිට 8% දක්වා විය යුතුය. කෙසේ වෙතත්, චිත්රපටයේ ක්ෂණික හැකිලීමේදී, බහාලුම් සීමාවන් හේතුවෙන්, තිරස් සහ සිරස් දිශාවන් සම්පූර්ණයෙන්ම හැකිලීමට නොහැකිය. ගිවිසුම්ගත රටාව, පෙළ සහ තීරු කේතය නිවැරදිව යථා තත්ත්වයට පත් කිරීම සහතික කිරීම සඳහා, කන්ටේනරයේ හැඩය සලකා බැලීම සහ සැබෑ තත්ත්වය මත පදනම්ව නිවැරදි ප්රමාණය සහ විරූපණ අනුපාතය ගණනය කිරීම අවශ්ය වේ. තහඩු වැනි චිත්රපට සිලින්ඩරාකාර හැඩතලවලට පරිවර්තනය කිරීම සහ අතිච්ඡාදනය වන ප්රදේශ මැලියම් සමඟ මුද්රා තැබීම අවශ්ය වන තාප හැකිලීමේ ලේබල් සඳහා, බන්ධන ශක්තියට බලපෑම් නොකිරීමට මුද්රා තැබීමේ ප්රදේශවල කිසිදු චිත්රක හෝ පෙළක් නිර්මාණය නොකළ යුතු බව සැලකිල්ලට ගැනීම වැදගත්ය.
තීරු කේතය ස්ථානගත කිරීම
සාමාන්යයෙන්, තීරු කේතයේ ස්ථානගත කිරීමේ දිශාව මුද්රණ දිශාවට අනුකූල විය යුතුය, එසේ නොමැතිනම් එය තීරු කේත රේඛා විකෘති කිරීමට හේතු වන අතර එය ස්කෑන් කිරීමේ ප්රතිඵලවලට බලපාන අතර වැරදි කියවීමට හේතු වේ. මීට අමතරව, ලේබල් නිෂ්පාදනවල වර්ණ තේරීම හැකිතාක් පැල්ලම් වර්ණ කෙරෙහි අවධානය යොමු කළ යුතු අතර, සැබෑ තත්ත්වය අනුව සම්පූර්ණ හෝ හිස් බවට පත් කළ හැකි සුදු අනුවාදයන් නිෂ්පාදනය කිරීම අවශ්ය වේ. තීරු කේත වල වර්ණය සාම්ප්රදායික අවශ්යතා අනුගමනය කළ යුතුය, එනම්, තීරු සහ අවකාශයේ වර්ණ සංයෝජනය තීරු කේත වර්ණ ගැලපීමේ මූලධර්මයට අනුකූල විය යුතුය. මුද්රණ ද්රව්ය තෝරාගැනීම. තාප හැකිලීමේ ලේබල් මුද්රණය කිරීම කෙටියෙන් විශ්ලේෂණය කර ඇති අතර, මුද්රණ ක්රියාවලිය හොඳින් පාලනය කිරීමට අමතරව, ද්රව්යය එහි ගුණාත්මක භාවයේ තීරණාත්මක කාර්යභාරයක් ඉටු කරයි. එබැවින් සුදුසු ද්රව්ය තෝරා ගැනීම ඉතා වැදගත් වේ. තාප හැකිලීමේ ලේබලයේ යෙදුම් ක්ෂේත්රය, පිරිවැය, චිත්රපටයේ ලක්ෂණ, හැකිලීමේ ක්රියාකාරිත්වය, මුද්රණ ක්රියාවලිය සහ ලේබල් කිරීමේ ක්රියාවලි අවශ්යතා මත පදනම්ව චිත්රපට ද්රව්යයේ thickness ණකම තීරණය කරන්න. හැකිලීමේ චිත්රපට ලේබල් සෑදීමේ සාමාන්ය අවශ්යතාවය වන්නේ චිත්රපටයේ ඝනකම මයික්රෝන 50ක්, මයික්රෝන 45ක් සහ මයික්රෝන 40ක් සමඟින් මයික්රෝන 30ත් මයික්රෝන 70ත් අතර විය යුතුය. නිශ්චිත ඝණකම ලේබල් කිරීමේ උපකරණවල ලේබල් කිරීමේ කාර්යසාධනය මත රඳා පවතී. තෝරාගත් ලේබල් ද්රව්ය සඳහා, චිත්රපට ද්රව්යයේ හැකිලීමේ අනුපාතය යෙදුම් පරාසය තුළ තිබීම සාමාන්යයෙන් අවශ්ය වන අතර තීර්යක් (TD) හැකිලීමේ අනුපාතය කල්පවත්නා (MD) හැකිලීමේ අනුපාතයට වඩා වැඩි වේ. බහුලව භාවිතා වන ද්රව්යවල පාර්ශ්වික හැකිලීමේ අනුපාතය 50% සිට 52% දක්වා සහ 60% සිට 62% දක්වා වන අතර විශේෂ අවස්ථා වලදී 90% දක්වා ළඟා විය හැකිය. කල්පවත්නා හැකිලීමේ අනුපාතය 6% සහ 8% අතර විය යුතුය. මීට අමතරව, හැකිලීමේ චිත්රපටයේ තාපය සඳහා ඉහළ සංවේදීතාවයක් හේතුවෙන්, ගබඩා කිරීම, මුද්රණය කිරීම සහ ප්රවාහනය කිරීමේදී අධික උෂ්ණත්වයන් වළක්වා ගැනීම වැදගත් වේ.
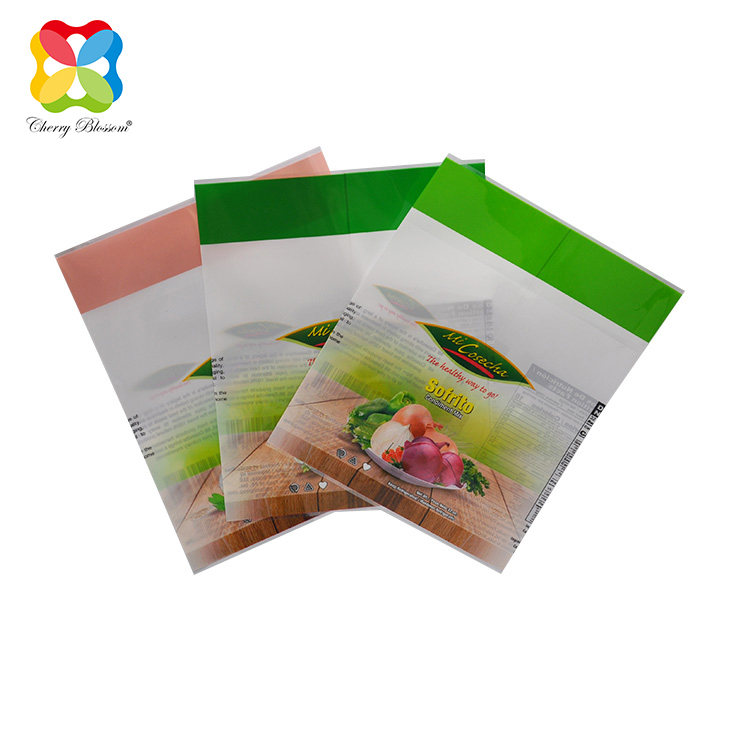
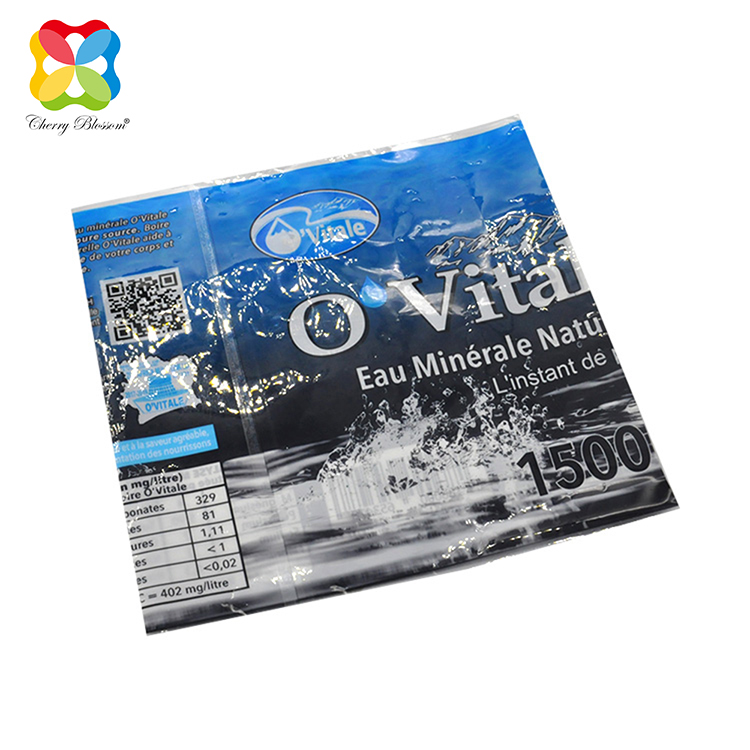
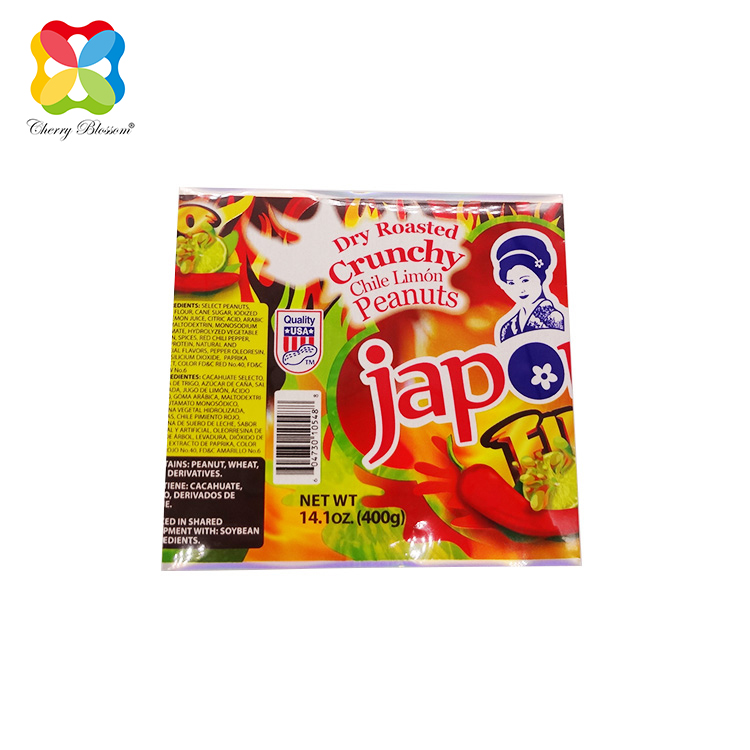
අත්යාවශ්ය මුද්රණය කිරීම
කඩදාසි ලේබල් මෙන් නොව, තාපය හැකිලීමේ පටලය අවශෝෂණ නොවන මුද්රණ ද්රව්ය භාවිතා කරයිPVC, PP, PETG, OPS, OPP, සහ විවිධ බහු-ස්ථර සම නිස්සාරණ චිත්රපට. මෙම ද්රව්යවල ගුණ තීරණය වන්නේ ඒවායේ මුද්රණ ක්රියාවලිය කඩදාසි ලේබල් වලින් වෙනස් වන බවයි. සාම්ප්රදායික ඕෆ්සෙට් මුද්රණය, ෆ්ලෙක්සොග්රැෆික් මුද්රණය (ෆ්ලෙක්සොග්රැෆික් මුද්රණය), ග්රේව් මුද්රණය සහ සේද තිර මුද්රණයේදී, තාප හැකිලීමේ චිත්රපට ලේබලවල මුද්රණ ක්රමය තවමත් ප්රධාන වශයෙන් ග්රැවර් මුද්රණය වේ. ප්රධාන හේතුව ගෘහස්ථ මුද්රණ යන්ත්ර විශාල ප්රමාණයක් තිබීම සහ මුද්රණ පිරිවැය සඳහා තරඟය දැඩි වීමයි. මීට අමතරව, gravure මුද්රණ නිෂ්පාදන ඝන තීන්ත තට්ටුවක්, දීප්තිමත් වර්ණ සහ පොහොසත් ස්ථර වල ලක්ෂණ ඇති අතර, මෙම වර්ගයේ ලේබල් ප්රධාන වශයෙන් දිගු තහඩු මුද්රණය වේ. gravure මුද්රණයට තහඩු මිලියන ගණනකට ඔරොත්තු දිය හැකිය, එබැවින් විශාල මුද්රණ ධාරිතාවක් සහිත සජීවී කොටස් සඳහා, එය නිසැකවම වඩාත්ම ලාභදායී වේ. කෙසේ වෙතත්, වෙළඳපල තරඟකාරිත්වය තීව්ර වීම සහ ෆ්ලෙක්සොග්රැෆික් තහඩු සෑදීම, යන්ත්රෝපකරණ සහ තීන්ත වැනි තාක්ෂණික දියුණුවත් සමඟ, ෆ්ලෙක්සොග්රැෆික් මුද්රණ අනුපාතය වසරින් වසර වැඩි වෙමින් පවතී. නමුත් පාරිභෝගිකයාගේ දෘෂ්ටිකෝණයෙන් වඩාත් වැදගත් වන්නේ තත්ත්ව ප්රමිතීන් සපුරාලීම, පිරිවැය අඩු කිරීම සහ සුදුසු මුද්රණ ක්රමය තෝරා ගැනීමයි.
ආතතිය පාලනය කිරීම
මුද්රණ ක්රියාවලියේදී තුනී පටල ආතති වෙනස්කම් වලට ගොදුරු වීමේ වැඩි අවදානමක් ඇති නිසා, සාවද්ය ලියාපදිංචිය හේතුවෙන්, ස්ථායීතාවය සහ ආතතියේ සමතුලිතතාවය පවත්වා ගැනීම සඳහා මුද්රණ ක්රියාවලියේදී ආතතිය පාලනය කිරීම කෙරෙහි දැඩි අවධානයක් යොමු කිරීම වැදගත් වේ. චිත්රපටයේ වර්ගය සහ ආතන්ය ශක්තිය මත පදනම්ව ආතති ගැලපුම් ප්රමාණය තීරණය කළ යුතුය. නිදසුනක් ලෙස, චිත්රපටයේ ආතන්ය ශක්තිය දුර්වල නම් සහ ආතන්ය විරූපණයට ගොදුරු වේ නම්, ආතතිය සාපේක්ෂව කුඩා විය යුතුය; ශක්තිමත් ආතන්ය ශක්තිය සහිත චිත්රපට සඳහා, ආතතිය අනුරූපව වැඩි කළ හැක. යම් ආකාරයක චිත්රපටයක් සම්බන්ධයෙන්, චිත්රපටයේ පළල සහ ඝනකම ද ආතතියේ විශාලත්වය තීරණය කරන වැදගත් සාධක වේ. පුළුල් චිත්රපටවල පටු චිත්රපටවලට වඩා වැඩි ආතතියක් තිබිය යුතු අතර ඝන චිත්රපට තුනී පටලවලට වඩා වැඩි ආතතියක් ඇත.
Gravure heat shrink film ප්රධාන වශයෙන් ඒකක වර්ගයේ gravure මුද්රණ යන්ත්ර භාවිතා කරන අතර ඒවා දැන් ආතති ස්වයංක්රීය පාලන පද්ධති සහ ස්වයංක්රීය වර්ණ ලියාපදිංචි කිරීමේ පාලන පද්ධති වලින් සමන්විත වේ. වර්ණ ලියාපදිංචි කිරීමේ ලකුණු අතර මනින ලද දෝෂය මත පදනම්ව, මුද්රණ ක්රියාවලියේ ස්ථායී ආතතිය සහ අවසාන මුද්රණයේ නිරවද්යතාවය සහතික කිරීම සඳහා විසන්ධි කරන ප්රදේශය, මුද්රණ ප්රදේශය සහ වංගු කරන ප්රදේශයේ ආතතිය ස්වයංක්රීයව සකස් කරනු ලැබේ. ගොඩගැසී ඇති සහ ඒකක ආකාරයේ flexographic මුද්රණ යන්ත්ර සමඟ සසඳන විට, CI වර්ගයේ flexographic මුද්රණ යන්ත්ර flexographic heat shrink film භාවිතා කිරීම සඳහා වඩාත් සුදුසු වේ. මක්නිසාද යත්, මුද්රණ ක්රියාවලියේදී, සෑම වර්ණ කණ්ඩායමක්ම පොදු මුද්රණ බෙරයක් බෙදා ගන්නා අතර, උපස්ථර ද්රව්ය සහ මුද්රණ බෙරය තදින් සවි කර ඇති අතර, ආතතියේ කුඩා වෙනස්කම් ඇති අතර, ද්රව්යයේ කුඩා ආතන්ය විකෘතියක් සහ ඉහළ ලියාපදිංචි නිරවද්යතාවයක් ඇති වේ.
තීන්ත තෝරා ගැනීම
හැකිලීමේ චිත්රපට මුද්රණය සඳහා භාවිතා කරන ප්රධාන තීන්ත වර්ග හතරක් ඇත: ද්රාවක පාදක තීන්ත, ජලය මත පදනම් වූ තීන්ත, කැටායන UV තීන්ත සහ නිදහස් රැඩිකල් UV තීන්ත. යෙදුම අනුව, ද්රාවක පදනම් කරගත් තීන්ත හැකිලීමේ චිත්රපට ලේබල් මුද්රණ ක්ෂේත්රයේ ආධිපත්යය දරයි, ඉන්පසු ජලය මත පදනම් වූ තීන්ත සහ නිදහස් රැඩිකල් UV තීන්ත. කෙසේ වෙතත්, කැටායන UV තීන්ත ඒවායේ අධික මිල සහ මුද්රණයේ අපහසුතා හේතුවෙන් හැකිලීමේ චිත්රපට ක්ෂේත්රයේ බහුලව භාවිතා නොවේ. ද්රාවක පාදක තීන්ත ප්රධාන වශයෙන් ග්රේව් සහ ෆ්ලෙක්සොග්රැෆික් මුද්රණයේදී තාප හැකිලීමේ චිත්රපට සඳහා යොදා ගනී. විවිධ චිත්රපට විශේෂිත තීන්ත භාවිතා කළ යුතු අතර මිශ්ර කළ නොහැක. තීන්ත සමාගම් සාමාන්යයෙන් විවිධ ද්රව්යවලට අනුරූප වන තීන්ත සඳහා ද්රාවක අනුපාත තුනක් සපයයි: වේගයෙන් වියළීම, මධ්යම වියළීම සහ මන්දගාමී වියළීම. මුද්රණ කර්මාන්තශාලාවලට වැඩමුළු උෂ්ණත්වය සහ මුද්රණ වේගය වැනි සැබෑ නිෂ්පාදන තත්ත්වයන් මත පදනම්ව සුදුසු ද්රාවක අනුපාතය තෝරාගත හැක. මීට අමතරව, ජලය මත පදනම් වූ තීන්ත සහ UV තීන්ත ද භාවිතා කළ හැකිය. කෙසේ වෙතත්, භාවිතා කරන තීන්ත වර්ගය කුමක් වුවත්, තීන්තවල කාර්ය සාධන දර්ශක අවශ්යතා සපුරාලිය යුතු බව සම්පූර්ණයෙන්ම සලකා බැලීම අවශ්ය වේ. උදාහරණයක් ලෙස, තීන්ත හැකිලීමේ අනුපාතය තාප හැකිලීමේ පටලයේ හැකිලීමේ ලක්ෂණ වලට අනුරූප විය යුතුය, එසේ නොමැතිනම් එය තීන්ත තට්ටුව බෙදීමට හෝ ඩීන්ක් කිරීමට පවා හේතු විය හැක.
වියළන උෂ්ණත්වය පාලනය කිරීම
තාපය හැකිලීමේ චිත්රපට මුද්රණය කිරීමේදී වියළන උෂ්ණත්වය හොඳින් පාලනය කිරීම ඉතා වැදගත් වේ. වියළන උෂ්ණත්වය ඉතා ඉහළ නම්, ද්රව්යය තාප හැකිලීම අත්විඳිනු ඇත; උෂ්ණත්වය ඉතා අඩු නම්, තීන්ත ප්රමාණවත් තරම් වියළී නොයනු ඇත, එහි ප්රතිඵලයක් වශයෙන් අවසාන ඇලවීම සහ පිටුපස අපිරිසිදු වේ. තීන්තවල එක් එක් වර්ණය සම්පූර්ණයෙන් වියළීම සහතික කිරීම සඳහා වර්ණ වියළන උපාංග gravure සහ flexographic මුද්රණ යන්ත්ර දෙකෙහිම ස්ථාපනය කර ඇත. ඒ අතරම, වියලීමේ ක්රියාවලියේදී ද්රව්යයේ විරූපණය වැළැක්වීම සඳහා, අවශේෂ තාපයේ බලපෑම පාලනය කිරීම සඳහා වර්ණ තට්ටු අතර සීතල වායු නාලිකා සැකසීම අවශ්ය වේ. වර්තමානයේ, මුද්රණ යන්ත්රවල ශීත කළ බෙර භාවිතා කරන අතර එමඟින් මුද්රණ ක්රියාවලියේදී ද්රව්යවල උෂ්ණත්වය ඉක්මනින් අඩු කළ හැකිය. ප්රබල රසායනික ස්ථායීතාවය, අඩු පෘෂ්ඨීය ශක්තිය, අවශෝෂණයකින් තොරව සුමට මතුපිටක් සහ මුද්රණ තීන්ත සමඟ ඇති දුර්වල සම්බන්ධතාවය වැනි හැකිලීමේ චිත්රපටවල පොදු මුද්රණ යෝග්යතාවය හේතුවෙන්. එබැවින්, භාවිතා කරන ලද මුද්රණ ක්රමය කුමක් වුවත්, චිත්රපටයේ මතුපිට ශක්තිය සහ රළුබව වැඩි දියුණු කිරීම සඳහා සහ ද්රව්ය මතුපිට තීන්තවල ඇලීමේ වේගවත් බව වැඩි දියුණු කිරීම සඳහා මතුපිට කොරෝනා විසර්ජන ප්රතිකාරය සිදු කළ යුතුය.
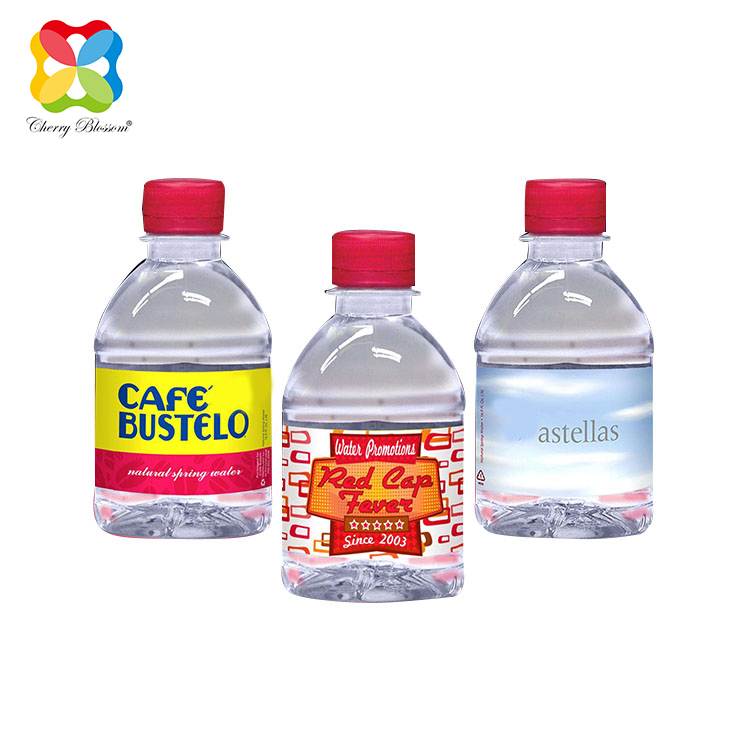

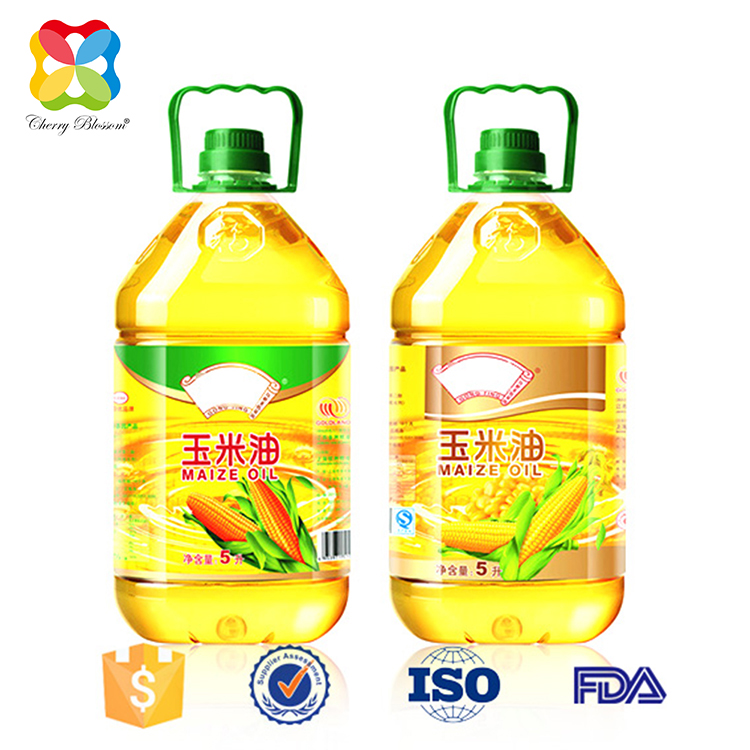
පසු කාලය: ජනවාරි-25-2024